Reconstruire le Cœur Numérique : Modernisation des Systèmes Hérités dans l’Industrie Manufacturière
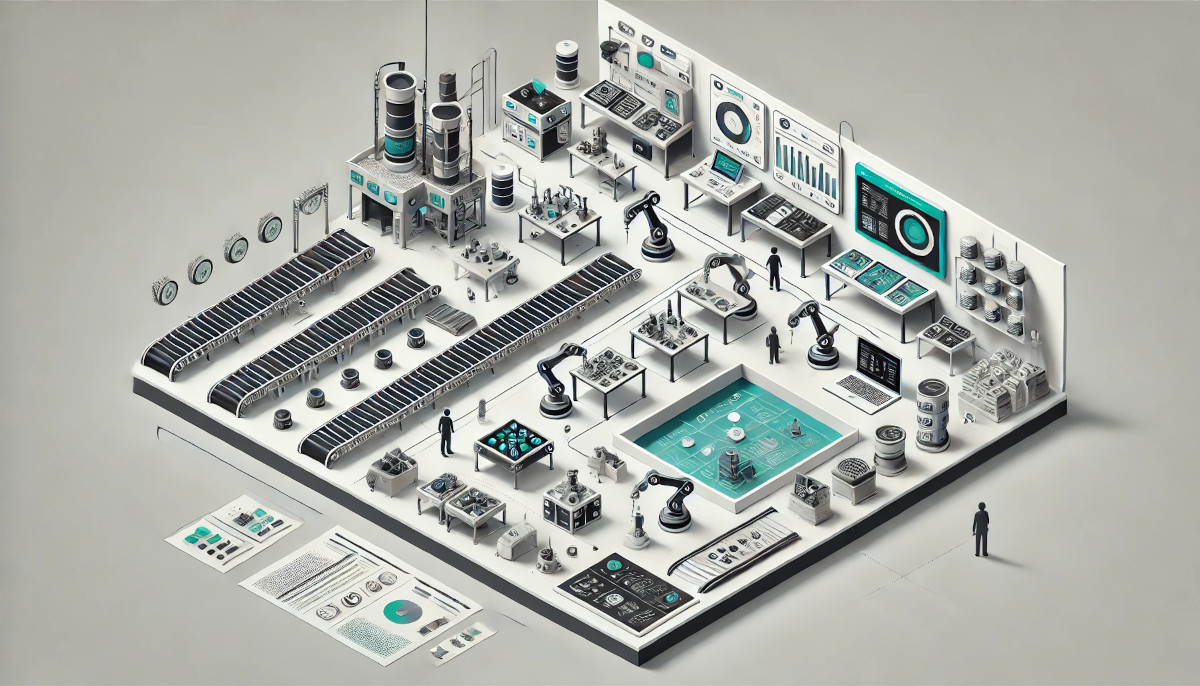
Agilité Industrielle vs Inertie Informatique
Les industriels du monde entier investissent dans la transformation numérique : usines intelligentes, maintenance prédictive, automatisation de la chaîne d’approvisionnement. Pourtant, nombre d’entre eux continuent de s’appuyer sur une infrastructure numérique vieillissante. Des systèmes d’exécution de production (MES) aux contrôleurs logiques programmables (PLC) basés sur du code hérité, ces plateformes—autrefois à la pointe—freinent désormais l’innovation, l’efficacité et l’agilité.
À l’heure où les exigences d’Industry 4.0 s’intensifient, les systèmes hérités s’avèrent inadaptés aux modèles opérationnels modernes. La modernisation n’est plus un projet informatique isolé : c’est une priorité stratégique pour les fabricants souhaitant rester compétitifs dans une économie automatisée et axée sur les données.
Technologie Héritée dans l’Industrie : De Pilier à Goulot d’Étranglement
Les systèmes hérités sont omniprésents dans les environnements industriels. Beaucoup d’installations reposent encore sur des logiciels écrits en COBOL, RPG ou en langage ladder pour faire fonctionner des systèmes critiques comme :
- SCADA (systèmes de contrôle et d’acquisition de données)
- MES (systèmes d’exécution de la production)
- MRP (planification des besoins en matières)
- QMS (systèmes de gestion de la qualité)
- Systèmes de logistique et d’inventaire
Conçus à une époque où l’intégration, la connectivité cloud et la visualisation en temps réel n’étaient pas prioritaires, ces systèmes forment aujourd’hui des silos freinant la prise de décision et la coordination opérationnelle.
Les problèmes majeurs incluent :
- Fragmentation des données empêchant une vue unifiée de l’usine
- Incompatibilité avec les plateformes cloud ou IoT, retardant la transition vers les usines intelligentes
- Coûts de maintenance élevés dus à des technologies dépassées et à des compétences rares
- Risque de panne lié à des logiciels non pris en charge et à une documentation manquante
Les systèmes hérités sont ainsi devenus le principal obstacle dans la chaîne de valeur manufacturière.
Conformité et Sécurité : Catalyseurs de Transformation
Au-delà de la productivité, la conformité réglementaire devient un moteur puissant de modernisation. Les standards évoluent rapidement, et les systèmes anciens peinent à répondre aux exigences en matière de qualité, de sécurité et d’environnement.
ISO 9001:2025 – Systèmes de management de la qualité
Ce standard renforce les attentes en matière d’analyse temps réel, de traçabilité et de prise de décision basée sur les données. Les QMS hérités, souvent locaux et rigides, ne peuvent y répondre sans modernisation.
Modernisation OSHA de la sécurité industrielle
Les anciens systèmes MES ne permettent pas d’intégrer d’alertes de défaillance prédictive, générant des risques accrus sur le terrain. Moderniser permet d’intégrer des systèmes d’analyse en amont des incidents.
Suivi des émissions EPA
Les sites industriels dotés de PLC anciens et de capteurs analogiques ne peuvent assurer un suivi continu des émissions. Or, les normes environnementales exigent désormais une surveillance automatisée et traçable.
Les systèmes non conformes exposent les entreprises à des amendes, des fermetures de site ou une perte de certification.
Le Coût Réel des Systèmes Hérités
La modernisation a un coût, mais maintenir des systèmes obsolètes en a un bien plus élevé. Les pertes se mesurent en argent, en temps, mais aussi en opportunités manquées.
Pertes liées aux interruptions
Un arrêt non planifié sur une ligne de production peut coûter jusqu’à 5 600 $ par minute. Les systèmes anciens, souvent instables, sont l’une des principales causes de ces interruptions.
Défauts qualité et rebuts
Les systèmes obsolètes n’intègrent pas d’analyse en temps réel, ce qui accroît les taux de rebut. Les fabricants perdent en moyenne 850 000 $ par an et par ligne en coûts liés à la qualité.
Dépendance aux compétences rares
La maintenance des systèmes hérités dépend d’ingénieurs expérimentés proches de la retraite. Leur départ entraîne une perte de savoir critique et des retards dans les opérations.
Coût d’opportunité
Les systèmes anciens bloquent l’adoption de la maintenance prédictive, de l’analytique IA ou de l’ordonnancement intelligent. Ces outils sont aujourd’hui indispensables à la compétitivité.
Moderniser permet de réduire ces coûts cachés et de libérer la croissance future.
CodeAura pour l’Industrie : Une Modernisation Intelligente et Progressive
CodeAura propose une plateforme alimentée par l’IA, pensée pour moderniser les systèmes industriels en alliant performance, sécurité et évolutivité. Notre approche tient compte des réalités du terrain et permet de transformer les infrastructures sans perturber la production.
Documentation assistée par IA
De nombreux systèmes industriels dépendent de connaissances tribales non documentées. CodeAura génère automatiquement des cartographies de code et des documents techniques exploitables, facilitant la formation, l’audit et la reprise d’activité.
Migration intelligente du code
Nous convertissons les bases COBOL, RPG ou ladder logic vers des architectures modernes, tout en conservant la logique de contrôle et en facilitant l’intégration avec le cloud, l’ERP ou les plateformes IoT.
Conformité intégrée
La plateforme intègre des outils de suivi ISO, OSHA et EPA dans le processus de modernisation. Elle assure la continuité des audits et la traçabilité des actions correctives.
Assistant IA en temps réel (Elliot)
Elliot fournit des informations système en temps réel aux opérateurs, ingénieurs et équipes qualité. Il aide à diagnostiquer une anomalie, valider une configuration ou anticiper un écart réglementaire.
CodeAura permet aux industriels de moderniser en toute confiance, sans ralentir la production.
Une Feuille de Route Stratégique
Une modernisation réussie repose sur une méthode structurée et progressive. Voici les étapes clés :
- Prioriser les systèmes critiques: Identifier les lignes ou processus à fort impact (arrêts fréquents, non-conformité, rebuts élevés).
- Moderniser par étapes: Éviter la refonte totale. Refactoriser les composants de manière modulaire pour maintenir la continuité.
- S’appuyer sur l’IA: Automatiser la documentation, la migration de code et la validation pour accélérer les délais et combler le déficit de compétences.
- Aligner avec l’Industrie 4.0/strong>: Intégrer la modernisation dans les projets de transformation digitale : jumeaux numériques, IA, automatisation avancée.
- Choisir un partenaire double-compétence: Privilégier un prestataire maîtrisant à la fois les systèmes industriels et les environnements techniques anciens.
Transformer l’Héritage en Atout
Les systèmes hérités représentent à la fois un défi et une opportunité. Bien qu’ils freinent l’innovation, ils contiennent des décennies de savoir métier précieux. L’enjeu est de préserver cette valeur tout en construisant l’usine de demain.
CodeAura permet d’y parvenir : une modernisation modulaire, automatisée et conforme, qui transforme la dette technique en levier de performance.
Modernisez avec CodeAura. Faites entrer votre usine dans l’ère intelligente. Réservez Une Démo Avec Nous.