Rebuilding the Core: Legacy System Modernization in Manufacturing
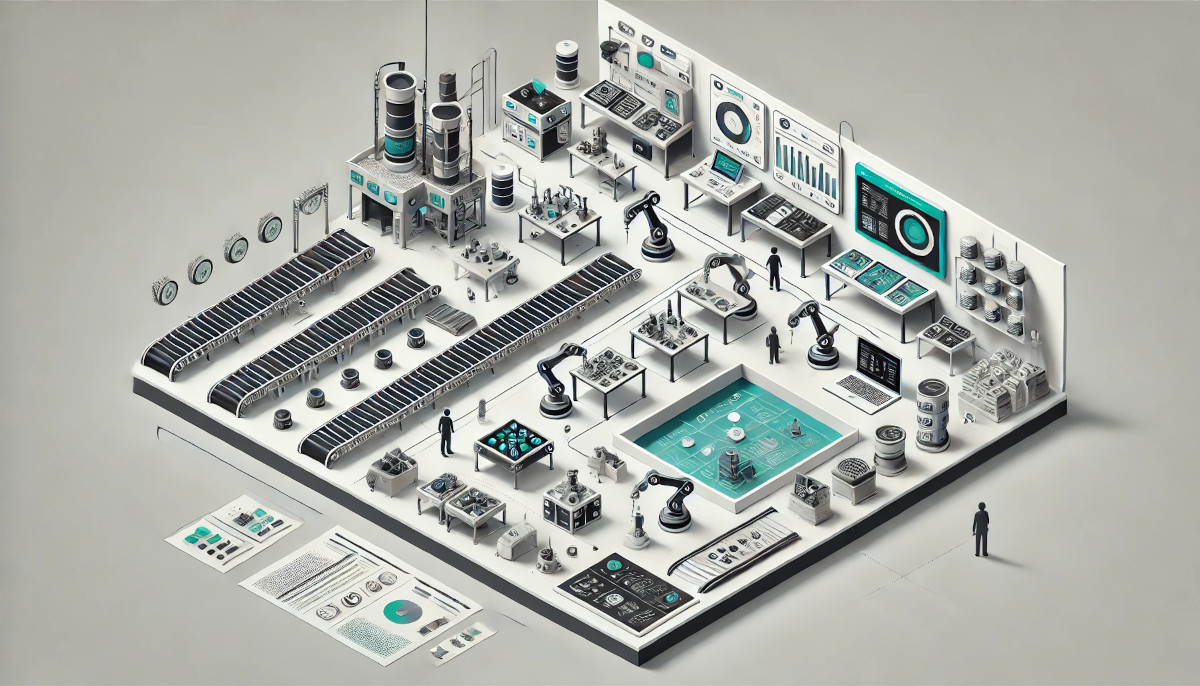
Industrial Agility Meets IT Inertia
Manufacturers across the globe are embracing digital transformation—investing in smart factories, predictive maintenance, and supply chain automation. However, many of these same organizations continue to operate on aging digital infrastructure built decades ago. From monolithic manufacturing execution systems (MES) to programmable logic controllers (PLCs) running legacy code, these systems—once revolutionary—now hinder innovation, efficiency, and agility.
As the demands of Industry 4.0 intensify, legacy platforms are proving incompatible with modern operational models. Modernization is no longer a back-office IT project. It is a strategic mandate for manufacturers seeking to remain competitive in an increasingly automated and data-driven economy.
Legacy Technology in Manufacturing: From Backbone to Bottleneck
Legacy systems are deeply embedded in manufacturing environments. Many facilities still rely on software written in COBOL, RPG, or proprietary ladder logic to run mission-critical systems like:
- Supervisory Control and Data Acquisition (SCADA) systems
- Manufacturing Execution Systems (MES)
- Material Requirements Planning (MRP) systems
- Quality Management Systems (QMS)
- Inventory and logistics platforms
These systems were designed in an era when integration, cloud connectivity, and real-time data visualization were not priorities. Today, they form fragmented silos that delay decision-making and prevent seamless process orchestration.
Key challenges include:
- Data fragmentation across siloed systems, limiting enterprise-wide visibility
- Incompatibility with cloud or IoT platforms, slowing smart factory adoption
- Excessive maintenance costs and reliance on aging, scarce developer talent
- Downtime risks due to unsupported software and undocumented components
In short, legacy technology has become the bottleneck in the modern manufacturing value chain.
Compliance and Safety Standards Driving Change
Beyond productivity, compliance is emerging as a powerful catalyst for modernization. Regulatory frameworks are evolving rapidly, and legacy systems are increasingly ill-suited to meet new operational, safety, and environmental standards.
ISO 9001:2025 – Quality Management Systems
This standard emphasizes data-driven decision-making, traceability, and real-time analytics. Legacy QMS systems, especially those built on on-premise or spreadsheet-based platforms, are unable to fulfill these requirements.
OSHA Safety Modernization
Outdated MES platforms often lack the ability to integrate predictive failure alerts, creating safety blind spots on the factory floor. Modernization enables integration with AI-based anomaly detection, helping prevent incidents before they occur.
EPA Emissions Monitoring
Manufacturers with aging PLCs and analog controls face increasing pressure to automate emissions tracking. Real-time monitoring and reporting are difficult—or impossible—without upgrading or retrofitting legacy systems.
As compliance becomes more technical and real-time in nature, the risks of inaction—from fines to production shutdowns—are growing rapidly.
The True Cost of Legacy in Manufacturing
While modernization often carries a significant upfront investment, the long-term costs of maintaining legacy infrastructure are far more substantial. These include not only direct financial costs, but also opportunity costs and productivity losses.
Downtime Losses
Unplanned downtime on a production line can cost up to $5,600 per minute—a figure that multiplies across multi-line operations and multiple sites. Legacy systems, due to their fragility and complexity, are a leading contributor to these disruptions.
Quality Defects and Rework
Outdated systems lack real-time analytics and anomaly detection, leading to higher defect rates. On average, manufacturers incur $850,000+ per year per line in quality-related costs due to inadequate data visibility and delayed responses.
Workforce and Skill Gaps
Legacy system maintenance often depends on a shrinking group of senior engineers familiar with proprietary platforms. As these professionals retire, manufacturers face knowledge loss, increased recruiting costs, and delayed system recovery.
Opportunity Costs
Outdated systems impede adoption of predictive maintenance, AI-powered analytics, and dynamic scheduling. These technologies are no longer optional—they are essential for competing in a globalized, just-in-time manufacturing environment.
Modernization enables organizations to reclaim these lost opportunities and invest in future-facing capabilities.
CodeAura in Manufacturing: Intelligent Modernization at Scale
CodeAura offers an AI-powered platform purpose-built to help manufacturers modernize legacy systems with precision, speed, and minimal disruption. Our solution addresses the unique constraints and complexity of industrial environments, empowering teams to transform their infrastructure incrementally and securely.
AI-Assisted Documentation
Many manufacturing systems suffer from tribal knowledge—key logic resides in the minds of senior engineers or buried in undocumented code. CodeAura automatically generates technical documentation and control logic maps for legacy systems, reducing onboarding time and ensuring business continuity.
Intelligent Code Migration
Our platform supports the migration of legacy codebases (including COBOL, RPG, and PLC logic) into modern, modular architectures. We preserve business rules and control logic while enabling seamless integration with modern platforms like cloud ERP, digital twins, and IoT analytics.
Compliance-Ready Transformation
CodeAura incorporates built-in compliance mapping to align system upgrades with ISO, OSHA, and EPA requirements. This allows for audit trail continuity and faster certification renewals—without the burden of manual documentation.
Real-Time System Intelligence with Elliot
“Elliot,” our AI assistant, provides real-time system insights to operators, engineers, and quality teams. Whether troubleshooting a production anomaly or validating compliance configurations, Elliot delivers contextual guidance derived from your actual code and infrastructure.
Together, these capabilities enable manufacturers to modernize with confidence—minimizing risk while maximizing operational outcomes.
A Strategic Modernization Roadmap for Manufacturers
Based on leading practices and real-world manufacturing constraints, a successful legacy modernization strategy includes the following components:
- Prioritize High-Impact Systems: Begin with production lines or control systems that have the highest incidence of downtime, quality issues, or compliance gaps.
- Adopt Incremental Modernization: Instead of full-system overhauls, refactor and upgrade components in a modular, phased approach. This reduces risk and ensures continuous operation.
- Leverage AI to Accelerate Outcomes: Use intelligent platforms to automate documentation, code translation, and compliance checks—bridging skill gaps and reducing time-to-value.
- Align Modernization with Industry 4.0 Goals: Legacy transformation should not be a siloed IT initiative. Link upgrades to strategic investments in automation, analytics, and smart factory initiatives.
- Choose Domain-Savvy Partners: Success hinges on working with modernization partners who understand both industrial operations and legacy technical environments. CodeAura bridges both worlds.
Turning Legacy into Leverage
Legacy systems in manufacturing represent both a challenge and an opportunity. While they constrain innovation and efficiency, they also contain years—sometimes decades—of embedded process knowledge. The key is to unlock that value without compromising operations.
CodeAura enables manufacturers to do just that. Our platform empowers teams to modernize intelligently, securely, and incrementally—transforming yesterday’s limitations into tomorrow’s competitive advantages.
Rebuild your digital core with CodeAura. Future-ready manufacturing begins here. Book a demo with us.